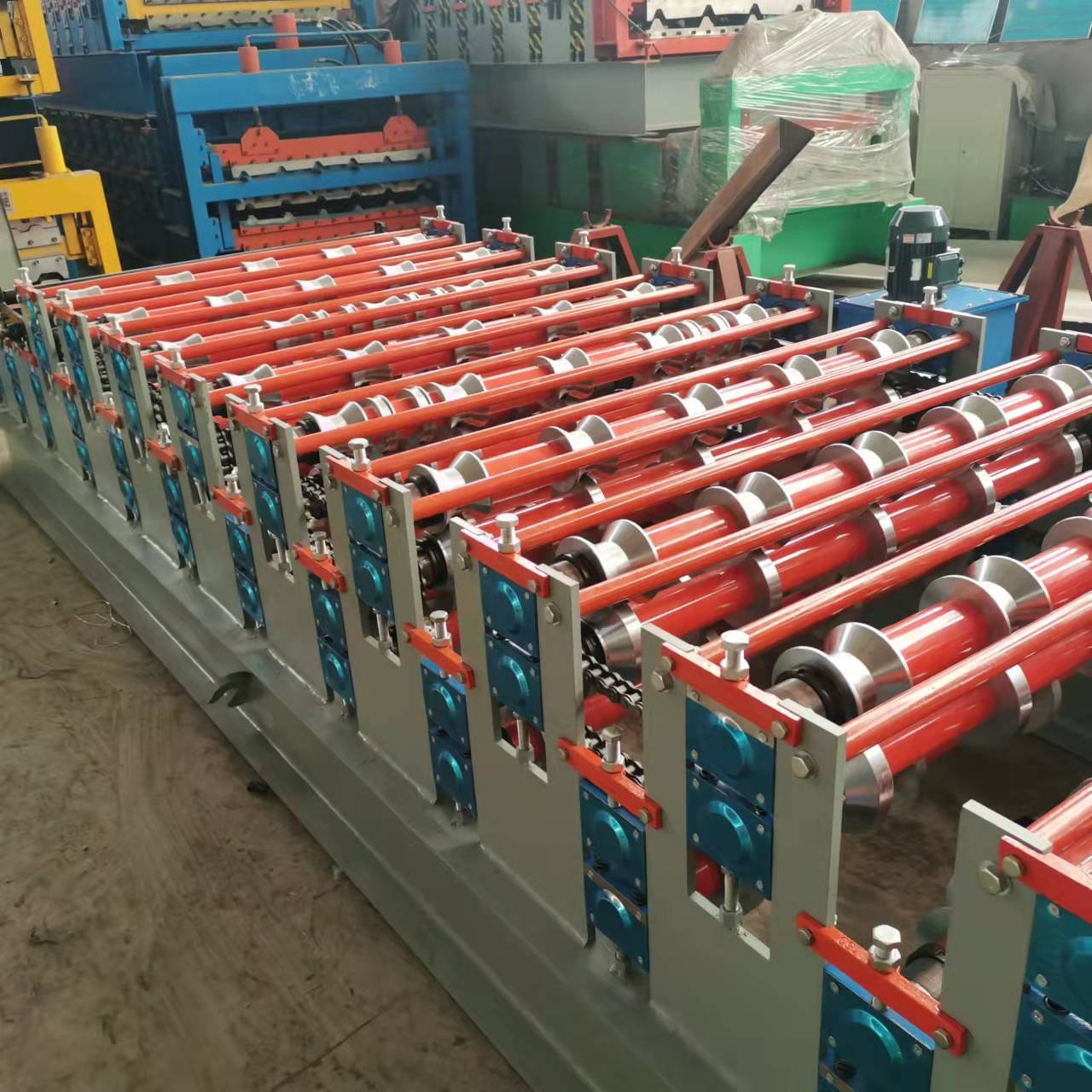
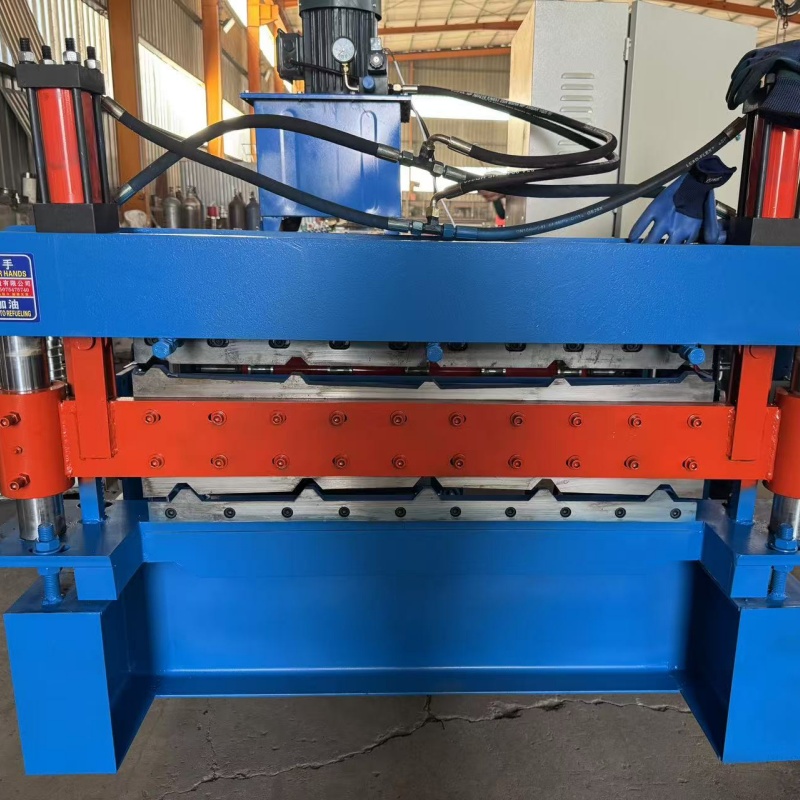
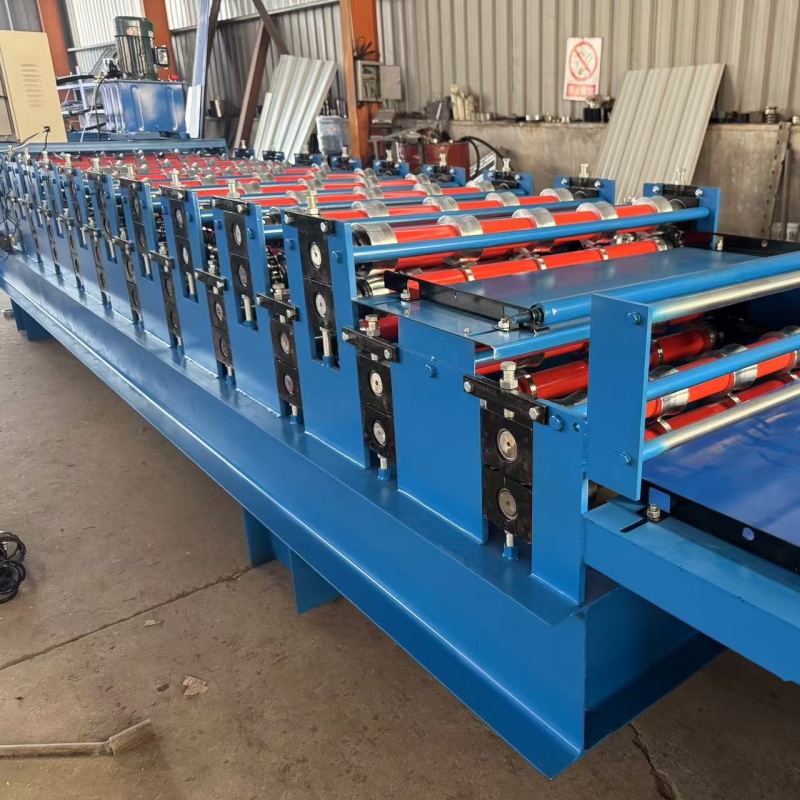
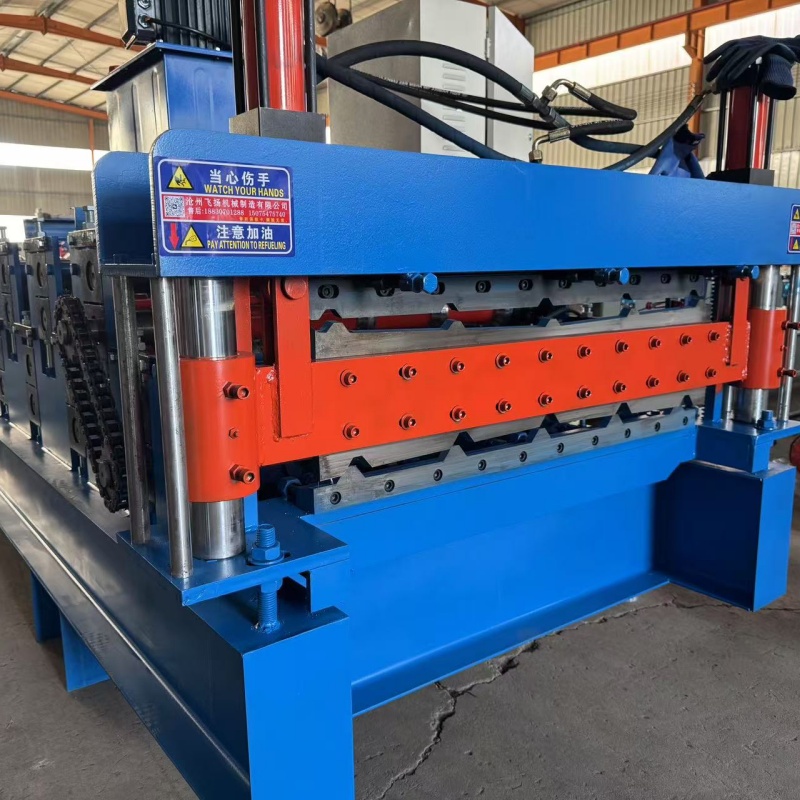
IBR and corrugated rollformer metal panel machine
Providing innovative machinery from IBR trapezoid to glazed tiles manufacturers.
Revolutionize roofing with innovative machinery.
Comprehensive support for enduring success.
Product Description
Introducing our cutting-edge IBR and corrugated rollformer metal panel machine! This powerful metal panel machine is designed to revolutionize your manufacturing process. With its advanced features, such as precision engineering and high-speed production, it ensures flawless results every time. Whether you're in the roofing or construction industry, this versatile machine is perfect for creating metal panels of various shapes and sizes. Its seamless integration and user-friendly interface allow for easy operation and increased productivity. Gain a competitive edge with our metal panel machine and experience the advantages of efficient production and superior quality.
Product Features
- IBR and corrugated rollformer: Our metal panel machine is capable of producing IBR and corrugated panels.
- High-quality metal panels: The machine ensures the production of durable and reliable metal panels.
- Efficient core extraction: The core can be easily extracted from the metal panels without any expansion, saving time and effort.
- Versatile usage: The machine is suitable for various applications, such as roofing, siding, and cladding.
- Compact design: With its compact size, the metal panel machine can fit into limited spaces, making it convenient for different work environments.
Application of metal panel machine
- Produces high-quality IBR and corrugated metal panels
- Efficiently forms metal panels for roofing and siding applications
- Perfect for residential, commercial, and industrial buildings
- Creates durable and weather-resistant metal panels
- Used in construction projects for a reliable and long-lasting roofing solution
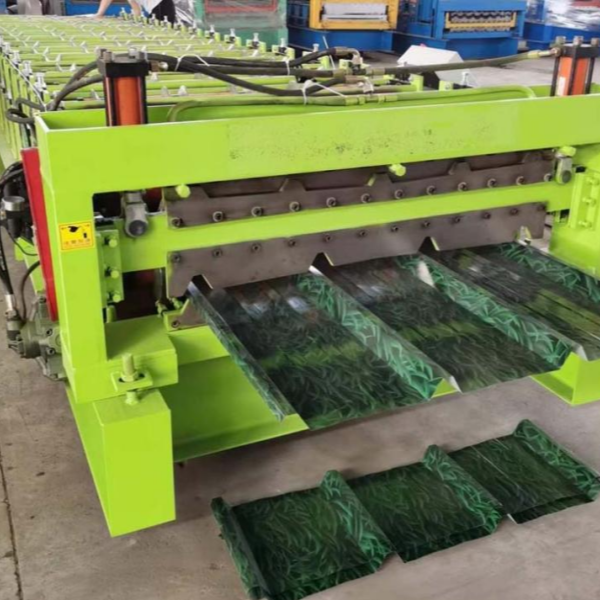
Hydraulic cutting device
This device for decking products cutting.Whole unit structure with steel plate welded,stable and strengthed.
With double guide pillar,ensure cutting process stable and smoothly.
Double cylinders,use steel oil pipe instead of rubber oil pipe,durable and beautiful.High strength sealing ring joint to avoid oil leakage.
Cutting blade base will be T type with milling machine processing for improving flatness,thereby extending the service life of the cutting tool.
Cutting blade material will be Cr 12Mov.
Quenched 58-60 to ensure hardness.
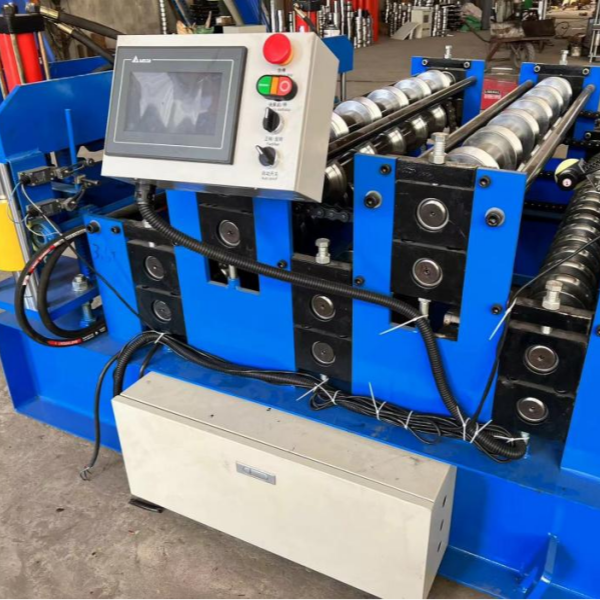
Electrical control system
Control Unit mainly for Delta,including 7inch HMI and PLC.
Low voltage Components:Delixi or schneider.
Frequency Changer/Inverter:ZONCN/Delta
Encoder Brand:Omron
All electrical brands are well-known domestic and foreign brands with 3C/CE/UL standard
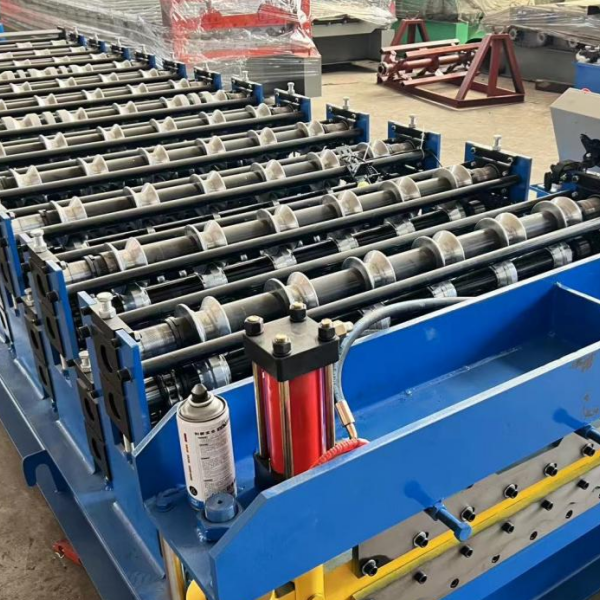
Roll forming machine
Frame main structure:H-beam.
Sidewall/Wallboard structure:14/16mm.
Shaft material:45# steel,solid shaft.Dia 70-75mm.
Roller shaft processing:Rough turning followed by precision turning,cylindrical grinding machine processing to ensure assembly accuracy,keyway processing to closely coordinate with the roller wheel for rotation.
Roller mold:45# steel .CNC lathing.
Transmission:Sprocket and chain
Driving Method:Reducer
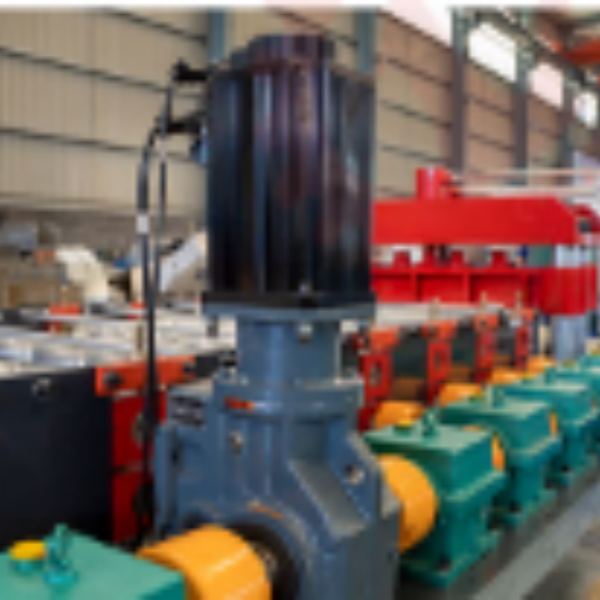
Drive system
We have close cooperation with well-known motor brands both domestically and internationally,such as Shanghai,Siemens,ABB,etc.Additionally,we recommend servo drive motors,for increasing production speed by more than 60%.
Transmission by gear and chain for stable working.Gear with quenched processing for long period production,1 inch chain for more stronger transmission,longer life,lower maintance cost.
The chain part is fully covered with protective cover for human safety.According to different design needs,gear box drive can be selected to make the machine run smoothly.
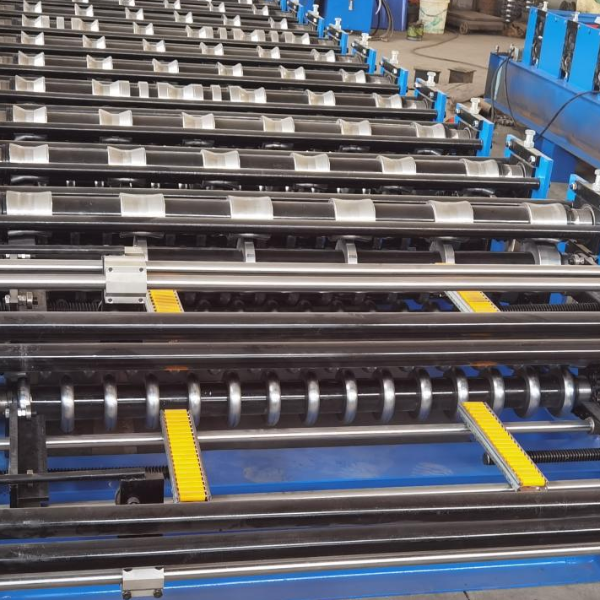
Feeding platform
Whole unit structure with steel plate welded,stable and strengthed.
There are material blocking square iron on the left and right sides to prevent the steel plate from deviating.Both sides are equipped with handles to adjust feeding width.
Feeding platform with position indicator used for record the position of the last feeding production,so that the production process can be traced.
Optional: We can add hydraulic front shear after the feeding platform and before forming the rollers,with the main purpose of calculating the overall production length and reducing waste generation.
Certificates
Our company in the "mechanical" industry takes great pride in the numerous industry certificates we have obtained over the years, which serve as a testament to our commitment to excellence and expertise. These certifications not only validate our dedication to quality, but also highlight our ability to meet and exceed industry standards. With our extensive knowledge and experience, we continuously strive to deliver cutting-edge products that are highly competitive in the market. By leveraging our industry certificates, we can confidently assure our customers that our offerings are backed by rigorous testing, superior craftsmanship, and the highest level of performance. Choosing our products means choosing reliability, durability, and innovation, making us the preferred choice in the industry.